광양 양극재 공장, 연산 9만 톤 생산
공장 자동화 통해 인력 사용 최소화
“배터리 시장 캐즘에도 설비 투자 지속”
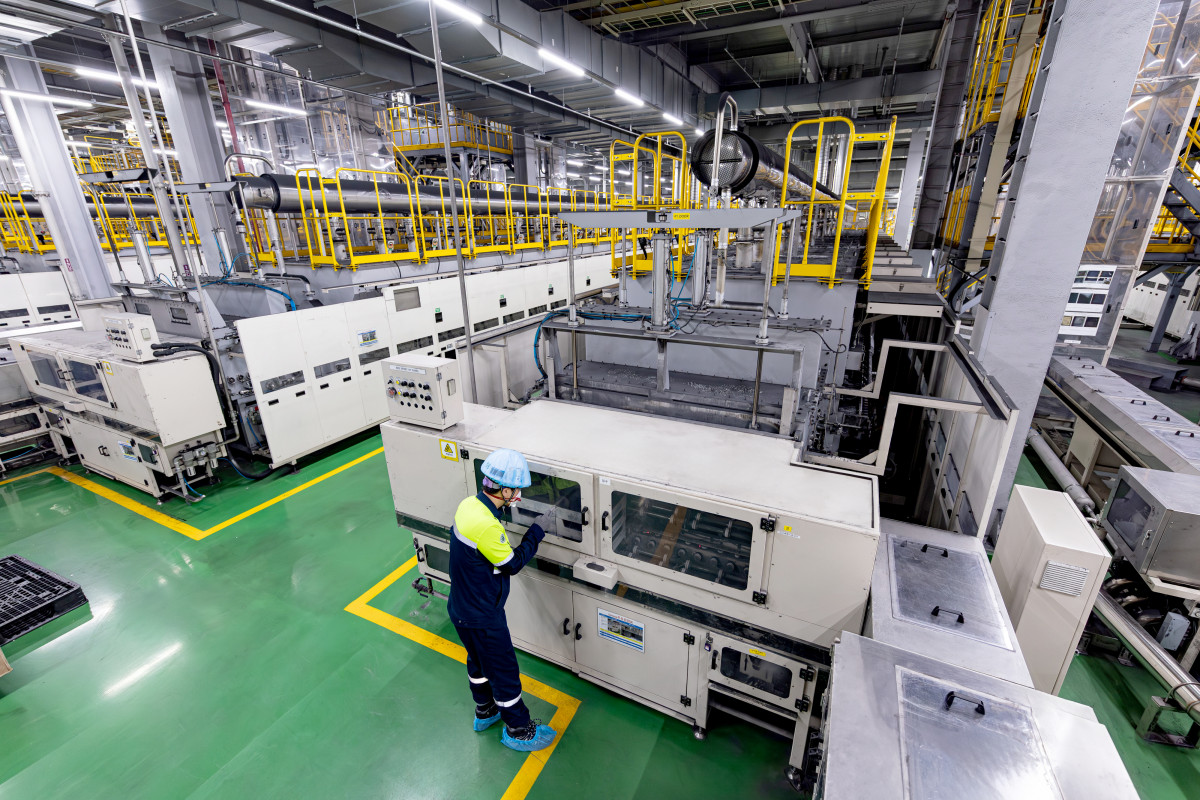
포스코 그룹은 본원 사업인 철강 부문 외에도 미래 먹거리인 이차전지 소재부문에서도 생산력 확대를 통한 경쟁력 향상에 매진하고 있다. 글로벌 배터리 시장 캐즘(일시적 시장정체기)에도 설비 투자를 지속하는 등 철강과 함께 그룹의 주력 성장엔진으로 만들겠다는 의지가 광양 공장 곳곳에서 엿보였다.
25일 찾은 포스코퓨처엠 광양 양극재 공장은 단일공장 기준 세계 최대 규모인 연산 9만 톤(t) 규모의 생산 능력을 갖추고 있다. 이는 60kWh 규모의 배터리가 탑재된 전기차 약 100만 대를 생산할 수 있는 양이다. 공장에는 13개의 생산라인이 갖추어져 있었다.
광양 양극재 공장은 니켈·코발트·망간(NCM), 니켈·코발트·알루미늄(NCA), 니켈·코발트·망간·알루미늄(NCMA) 등의 양극재를 생산한다. 지난해 3월부터는 국내 최초로 하이니켈 NCMA 단결정 양극재 양산을 시작했다. 양극재는 배터리의 4대 소재(양극재·음극재·전해액·분리막) 중 배터리 원가에서 가장 높은 비중인 약 40%를 차지하고 있다.
이러한 양극재를 생산하는 광양 양극재 1공장은 안전모, 고글, 마스크, 안전화 착용은 물론 신발 커버를 하고 에어 샤워까지 마쳐야 입장이 가능했다. 공정 관리상 이물질 관리가 민감한 사항이라 필수 조치라는 설명이 뒤따랐다.
광양 공장은 24시간 쉬지 않고 양극재를 만들고 있었다. 내부엔 양극재를 생산하기 위한 장비 라인들이 줄지어 배치돼 있었는데, 가장 먼저 눈에 띄는 것은 55m 길이의 소성로였다. 소성로는 열처리 시설로 양극재의 주요 원료에 열을 가해 섞는 역할을 수행한다.
포스코퓨처엠 관계자는 “고온의 열로 화학 반응을 일으키는 소성 공정이 메인이라고 할 수 있다”고 설명했다.
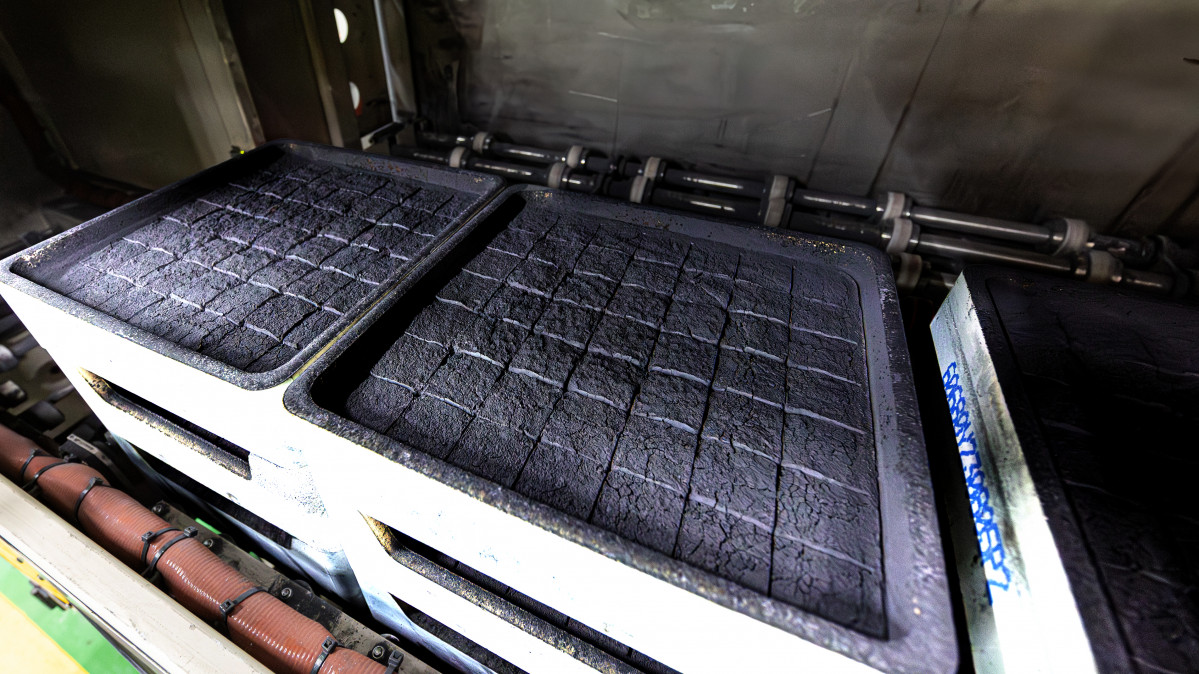
소성로 안에는 니켈, 리튬 등이 섞인 검은색 양극재 가루를 사각형 모양으로 담은 흰 도가니가 줄지어 옮겨지고 있었다. 공장 내에는 소성로 투입을 앞둔 도가니, 이미 들어갔다가 나온 도가니들이 대량으로 눈에 띄었다.
양극재가 만들어지는 데엔 약 3일 정도가 걸린다. 완성된 양극재와 그 외 필수 원료들은 공장 옆 자동화 창고로 옮겨진다. 창고로 옮기는 데에는 인력이 아닌 무인운반로봇(AGV)이 사용된다.
이처럼 양극재 생산 및 운반 과정에서 인력 사용은 보기 힘들었다. 현장에 있는 몇몇 직원들은 설비가 문제가 있는지 살펴보고 점검하는 정도였다. 근로자 안전 문제가 화두인 만큼 공장 자동화를 통해 인력의 위험 부담을 최소화하겠다는 포스코의 노력이 엿보였다.
자동화 창고는 약 1600평 규모로 이루어져 있다. 양극재 원료는 약 20m 높이의 선반에 층별로 쌓여 있었다.
이현우 포스코퓨처엠 기술용접부장은 “외부 물질에 취약한 양극재 특성 때문에 사람이 쉽게 다가갈 수 없고 습도와 온도가 철저히 유지되도록 관리 중이다”고 말했다.
이어서 방문한 자동화분석실에서는 원료, 반제품, 완제품 등 공정 전 단계에서 샘플을 채취한 후 공정별 기준에 맞는지 점검 및 분석하고 있었다. 하루 평균 500개 정도의 샘플을 채취한다. 샘플을 분석실로 보내는 데는 ‘에어 슈팅 시스템’을 이용하는데, 해당 시스템을 통해 1분 내외로 분석실에서 샘플을 받아볼 수 있다.
글로벌 배터리 시장이 캐즘에 빠졌지만, 광양 공장 인근 부지에서는 내년 하반기 준공을 목표로 연산 5만2500톤 규모 하이니켈 NCA 양극재 5공장 공사에 한창이다.
내년 상반기에 준공되면 포스코퓨처엠 광양 공장의 양극재 생산능력은 연산 14만2500톤으로 늘어나게 된다. 또 중국 항저우와 캐나다 퀘백에 각각 연산 2만5000톤, 3만 톤 규모의 양극재 공장을 건설하는 등 미래를 위한 투자에 적극 나서고 있다.
포스코퓨처엠은 관계자는 “글로벌 이차전지 시장의 캐즘에 개의치 않고 우량자원을 확보와 생산량 확대에 지속적인 투자를 하고, 차세대 소재 개발에 나서자는 것이 회사의 방침”이라고 말했다.
댓글0